Оперативная система управления токарным станком в системе ЧПУ Delta Electronics NC200
При изготовлении любых деталей точением часто возникает необходимость выполнить простую операцию — проточить поверхность или паз, просверлить отверстие, нарезать резьбу и другие. Более того, многие детали можно изготавливать, комбинируя такие простые операции, и для этого нет необходимости в привлечении программиста-технолога к написанию программ для систем ЧПУ.
Для обеспечения высокой точности изготовления деталей и производительности выполнение таких простых операций можно автоматизировать, используя оперативную систему управления станком (ОСУ, по-английски — EASY CNC). Такая возможность реализована в системе ЧПУ Delta NC200 компании Delta Electronics.
Применение ОСУ в системе ЧПУ Delta NC200 позволяет:
- выполнять в ручном режиме отдельные операции точения,
- формировать последовательность обработки детали в пошаговом режиме на основе базовых операций с последующим автоматическим выполнением этой последовательности,
- выполнять технологические циклы, основанные на линейной и круговой интерполяции,
- полностью изготавливать детали со сложной геометрией, содержащей галтели, конусы, сферы и разные резьбы,
- увеличить производительность работы по сравнению с универсальными станками в 2-5 раз за счет автоматического выполнения циклов обработки,
- сохранять в памяти множество подготовленных программ для обработки деталей.
Работать с ОСУ системы ЧПУ Delta NC200 может станочник абсолютно любой квалификации. Программа изготовления даже очень сложных по конфигурации изделий создается прямо на станке без привлечения технолога или высококвалифицированного оператора ЧПУ. Достаточно взять чертеж или эскиз детали, выбрать в ОСУ базовые циклы обработки детали в нужной последовательности и задать для каждой операции необходимый набор параметров.
Оперативная система ЧПУ Delta NC200 содержит 18 экранов со стандартными рабочими циклами и позволяет создать программу обработки с практически неограниченным количеством циклов.
Программный файл ограничен только недостижимым в реальной программе максимальным размером 5 Мбайт. Таким образом, станку с системой ЧПУ Delta NC200 под силу изготовить изделия даже очень сложной конфигурации.
Стандартные циклы обработки:
Наружная обработка |
Внутренняя обработка |
Торцевая обработка |
Наружный конус |
Внутренний конус |
Наружная резьба |
Внутренняя резьба |
Резьба метчиком |
Наружные пазы |
Внутренние пазы |
Торцевые пазы |
Сверление |
Внутренняя выпуклая |
Внешняя вогнутая |
Внешняя сфера |
Внутренняя сфера |
Экраны, позволяющие задать уникальную траекторию обработки:
Внешний контур обработки |
Внутренний контур обработки |
Создание программы изготовления детали, используя встроенные циклы обработки ОСУ системы ЧПУ Delta NC200
Подкупает простота перехода в режим ввода циклов обработки. Достаточно перейти в режим редактирования, нажав кнопку EDIT и затем дважды — программную кнопку PRG. Система, перейдя в экран файлового менеджера, предложит создать собственный проект с сохранением его на встроенной CF-карте.
Для примера рассмотрим подробно создание программы вытачивания профильного вала из круглой заготовки. Как уже отмечалось ранее, создание проекта начинается с экрана файлового менеджера.
Заходим на диск CF, где создаем новый проект, например, «TEST».
Зайдя в файл созданного проекта «TEST» система, помимо готовых шаблонов, предложит создать блоки инициализации «INITIAL» и финализации «FINISH». При необходимости в них можно добавить дополнительные движения осей или включение дополнительных функций станка. Блок инициализации — это часть программы, выполняемая до основного цикла, блок финализации — после окончания основного цикла.
Далее открываем экран шаблонов и выбираем необходимый цикл. В нашем случае это — «Наружная обработка».
При создании цикла пользователю необходимо ввести ряд параметров:
- X1, Z1 – координаты первой точки
- X2, Z2 – координаты второй точки
- X3, Z3 – координаты третьей точки
- X4, Z4 – координаты 4й точки
- Tx, Tz – координаты для смены инструмента
- Ud - глубина резания (X)
- Wm – настройки резания (0 – грубая + финишная; 1 – грубая; 2 – финишная)
- Rdx, Rdz – допуск по осям X, Z
- M – номер М-команды для подачи СОЖ
- T – номер инструмента для грубой обработки и его корректор
- G70_T – номер инструмента для финишной обработки
- F – скорость подачи для грубой обработки
- G70_F – скорость подачи для финишной обработки
- G92 – ограничение скорости шпинделя
- G (справа) – компенсация радиуса инструмента (40 – отключение компенсации, 41 – компенсация слева, 41 – компенсация справа)
- G (слева) – контроль скорости шпинделя (96 - постоянная скорость резания, 97 – постоянная скорость)
- S – скорость шпинделя
- M – направление вращения шпинделя.
В один проект можно добавить неограниченное количество циклов обработки в необходимой последовательности, тем самым создав сложную деталь, не отходя от станка:
После создания проекта система генерирует управляющую программу в G-коде:
Созданную программу можно проверить в режиме предпросмотра (Preview) на экране «Графика» (GRAPHICS):
Система позволяет запустить автоматическое выполнение программы (режим АВТО).
Но если оператор решить проконтролировать точение первого экземпляра изделия в ручном режиме, то его изготовление системе ЧПУ Delta NC200 возможно в режиме «MPG SIM», активация которого производится с помощью соответствующей кнопки, вынесенной на станочную панель.
При нажатии этой кнопки система останавливает автоматическое выполнение технологического цикла и предоставляет оператору возможность дальнейшего управления движением по траектории обработки в ручном режиме — как в прямом, так и в обратном направлении. При повторном нажатии кнопки «MPG SIM» система переходит обратно в автоматический режим выполнения технологической программы с текущей позиции.
Остальные циклы обработки заготовки применяются аналогично. Поэтому представим только параметры циклов на соответствующих экранах:
Внутренняя обработка
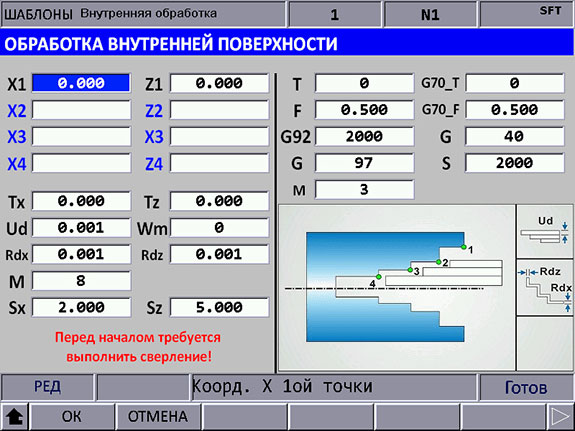 |
Торцевая обработка
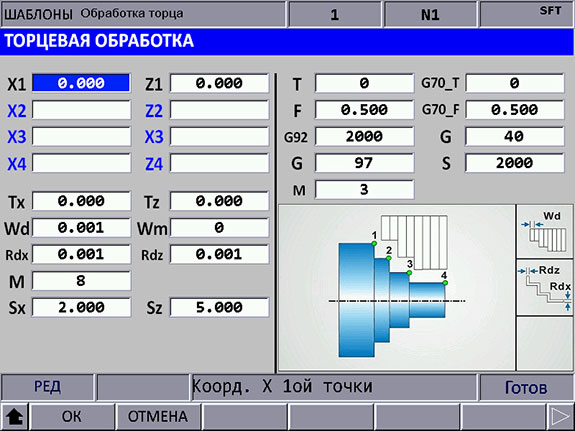 |
- X1, Z1 – координаты первой точки
- X2, Z2 – координаты второй точки
- X3, Z3 – координаты третьей точки
- X4, Z4 – координаты четвертой точки
- Tx, Tz – координаты для смены инструмента
- Ud - глубина резания (X)
- Wm – настройки резания (0 – грубая + финишная, 1 – грубая, 2 – финишная)
- Rdx, Rdz – допуск по X, Z
- M – номер М-команды для подачи СОЖ
- T – номер инструмента для грубой обработки и его корректор
- G70_T – номер инструмента для финишной обработки
- F – скорость подачи для грубой обработки
- G70_F – скорость подачи для финишной обработки
- G92 – ограничение скорости шпинделя
- G (справа) – компенсация радиуса инструмента (40 – отключение компенсации, 41 – компенсация слева, 41 – компенсация справа)
- G (слева) – контроль скорости шпинделя (96 - постоянная скорость резания, 97 – постоянная скорость)
- S – скорость шпинделя
- M – направление вращения шпинделя
|
Наружный конус
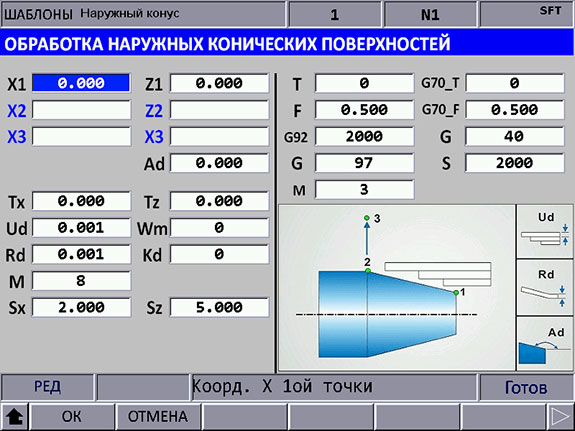 |
Внутренний конус
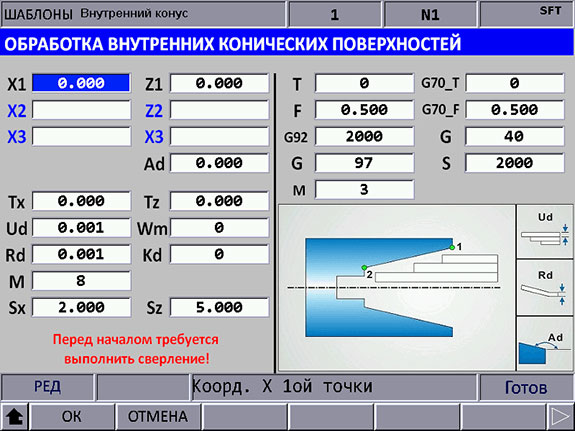 |
- X1, Z1 – координаты первой точки
- X2, Z2 – координаты второй точки
- X3, Z3 – координаты третьей точки
- Ad – угол конуса
- Tx, Tz – координаты для смены инструмента
- Ud - глубина резания (X)
- Wm – настройки резания (0 – грубая + финишная, 1 – грубая, 2 – финишная)
- Rd – допуск финишный
- Kd – формат конуса (0 – XZ, 1 – XA, 2 – ZA)
- M – номер М-команды для подачи СОЖ
- T – номер инструмента для грубой обработки и его корректор
- G70_T – номер инструмента для финишной обработки
- F – скорость подачи для грубой обработки
- G70_F – скорость подачи для финишной обработки
- G92 – ограничение скорости шпинделя
- G (справа) – компенсация радиуса инструмента (40 – отключение компенсации, 41 – компенсация слева, 41 – компенсация справа)
- G (слева) – контроль скорости шпинделя (96 - постоянная скорость резания, 97 – постоянная скорость)
- S – скорость шпинделя
- M – направление вращения шпинделя
|
Наружная резьба
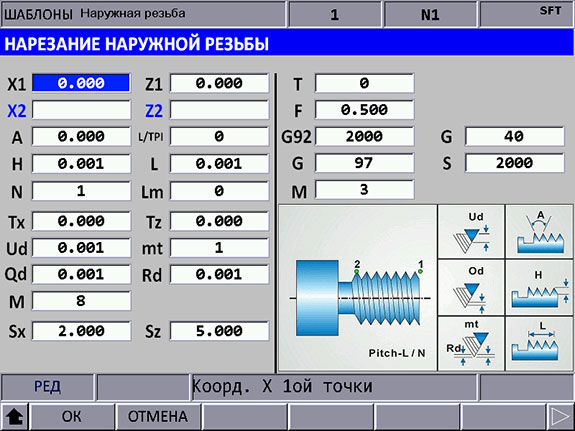 |
Внутренняя резьба
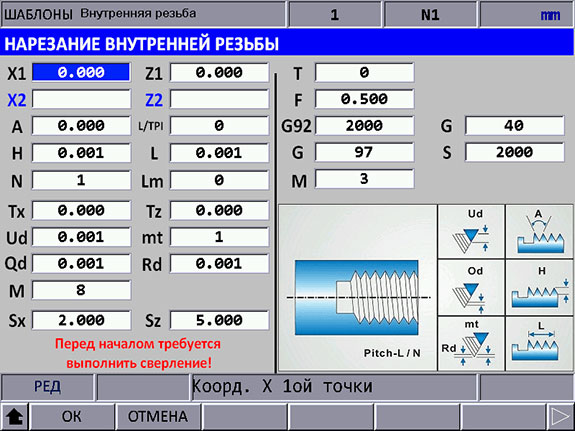 |
- X1, Z1 – координаты первой точки
- X2, Z2 – координаты второй точки
- A – угол резьбы
- L/TPI – 0 – длина резьбы, 1 – количество зубьев на дюйм.
- H – общая глубина резьбы
- L - если выше L, то мм/шаг, если выше TPI, то зубьев/дюйм
- N - количество витков
- Tx, Tz – координаты для смены инструмента
- Ud - первая глубина резания
- Mt – количество циклов финишной обработки
- Qd – минимальная глубина резания
- Rd – финишный допуск
- M – номер М-команды для подачи СОЖ
- T – номер инструмента для грубой обработки и его корректор
- F – скорость подачи для грубой обработки
- G92 – ограничение скорости шпинделя
- G (справа) – компенсация радиуса инструмента (40 – отключение компенсации, 41 – компенсация слева, 41 – компенсация справа)
- G (слева) – контроль скорости шпинделя (96 - постоянная скорость резания, 97 – постоянная скорость)
- S – скорость шпинделя
- M – направление вращения шпинделя
|
Наружные пазы
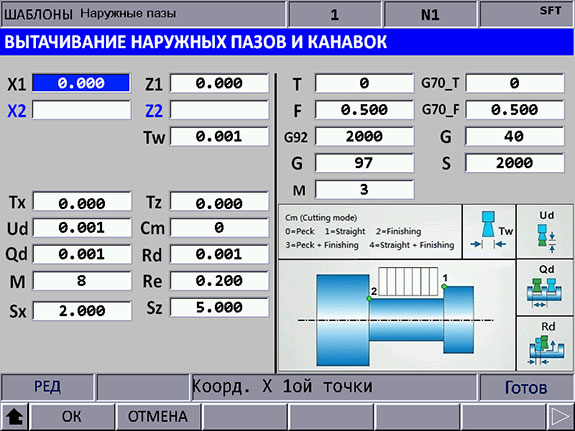 |
Внутренние пазы
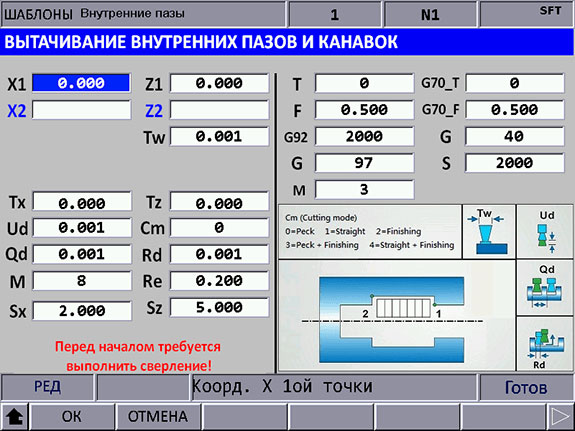 |
- X1, Z1 – координаты первой точки
- X2, Z2 – координаты второй точки
- Tw – ширина канавки инструмента
- Tx, Tz – координаты для смены инструмента
- Ud - глубина резания за шаг (X)
- Wm – выбор режима обработки (0 – послойная, 1 -прямая, 2 - финишная)
- Qd – ширина резания за шаг (Z)
- Rd – допуск по X, Z
- Re – рельеф, величина задержки на оси Z после того, как по оси Х завершилась резка
- M – номер М-команды для подачи СОЖ
- T – номер инструмента для грубой обработки и его корректор
- G70_T – номер инструмента для финишной обработки
- F – скорость подачи для грубой обработки
- G70_F – скорость подачи для финишной обработки
- G92 – ограничение скорости шпинделя
- G (справа) – компенсация радиуса инструмента (40 – отключение компенсации, 41 – компенсация слева, 41 – компенсация справа)
- G (слева) – контроль скорости шпинделя (96 - постоянная скорость резания, 97 – постоянная скорость)
- S – скорость шпинделя
- M – направление вращения шпинделя
|
Торцевые пазы
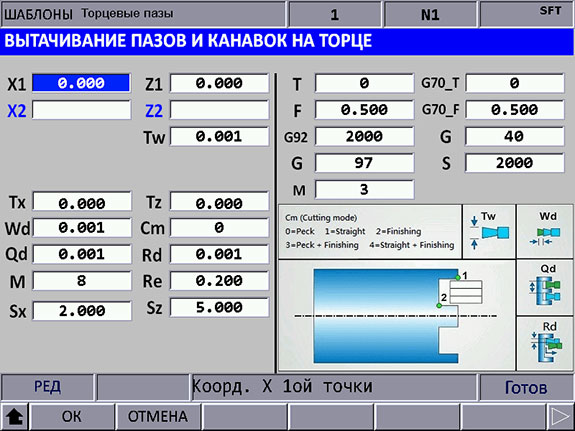 |
Сверление
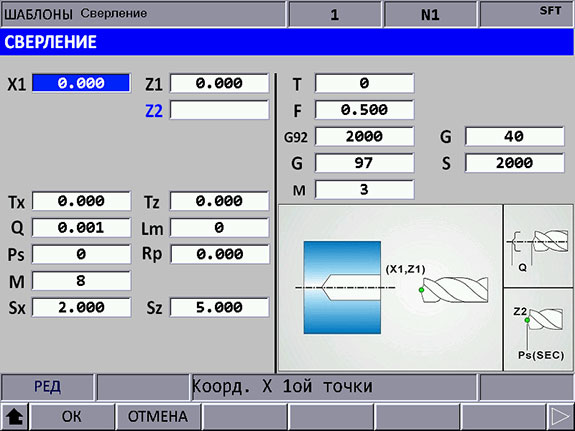 |
- X1, Z1 – координаты первой точки
- X2, Z2 – координаты второй точки
- Tw – ширина канавки инструмента
- Tx, Tz – координаты для смены инструмента
- Wd - глубина резания за шаг (Z)
- Wm – выбор режима обработки (0 – послойная, 1 -прямая, 2 - финишная)
- Qd – ширина резания за шаг (Z)
- Rd – допуск по X, Z
- Re – рельеф, величина задержки на оси Z после того, как по оси Х завершилась резка
- M – номер М-команды для подачи СОЖ
- T – номер инструмента для грубой обработки и его корректор
- G70_T – номер инструмента для финишной обработки
- F – скорость подачи для грубой обработки
- G70_F – скорость подачи для финишной обработки
- G92 – ограничение скорости шпинделя
- G (справа) – компенсация радиуса инструмента (40 – отключение компенсации, 41 – компенсация слева, 41 – компенсация справа)
- G (слева) – контроль скорости шпинделя (96 - постоянная скорость резания, 97 – постоянная скорость)
- S – скорость шпинделя
- M – направление вращения шпинделя
|
- X1, Z1 – координаты первой точки
- Z2 – координата второй точки
- Tx, Tz – координаты для смены инструмента
- Q - глубина резания (X)
- Wm – выбор режима обработки (0 – послойная, 1 -прямая, 2 - финишная)
- Ps – время задержки
- M – номер М-команды для подачи СОЖ
- T – номер инструмента для грубой обработки и его корректор
- F – скорость подачи для грубой обработки
- G92 – ограничение скорости шпинделя
- G (справа) – компенсация радиуса инструмента (40 – отключение компенсации, 41 – компенсация слева, 41 – компенсация справа)
- G (слева) – контроль скорости шпинделя (96 - постоянная скорость резания, 97 – постоянная скорость)
- S – скорость шпинделя
|
Внешняя сфера
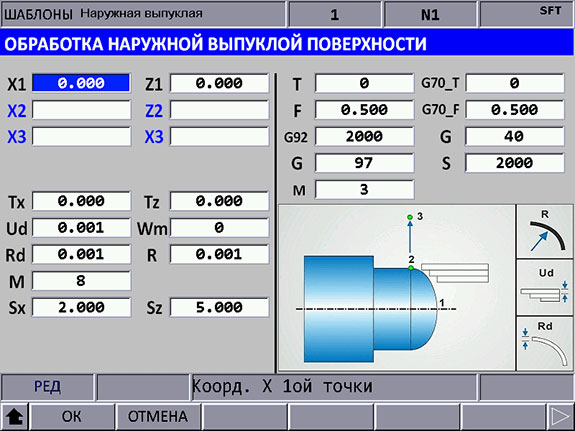 |
Внутренняя сфера
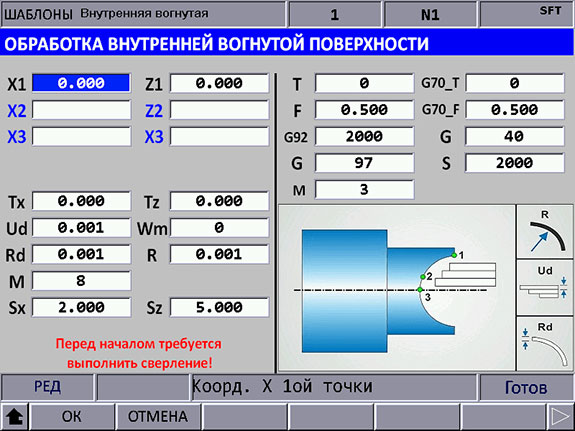 |
- X1, Z1 – координаты первой точки
- X2, Z2 – координаты второй точки
- X3, Z3 – координаты третьей точки
- Tx, Tz – координаты для смены инструмента
- Ud - глубина резания (X)
- Wm – настройки резания (0 – грубая + финишная, 1 – грубая, 2 – финишная)
- Rd– финишный допуск
- R – радиус дуги
- M – номер М-команды для подачи СОЖ
- T – номер инструмента для грубой обработки и его корректор
- G70_T – номер инструмента для финишной обработки
- F – скорость подачи для грубой обработки
- G70_F – скорость подачи для финишной обработки
- G92 – ограничение скорости шпинделя
- G (справа) – компенсация радиуса инструмента (40 – отключение компенсации, 41 – компенсация слева, 41 – компенсация справа)
- G (слева) – контроль скорости шпинделя (96 - постоянная скорость резания, 97 – постоянная скорость)
- S – скорость шпинделя
- M – направление вращения шпинделя
|
Внутренняя выпуклая поверхность
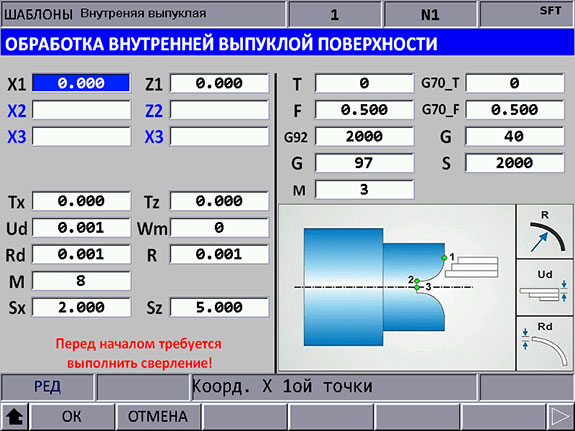 |
Внешняя вогнутая поверхность
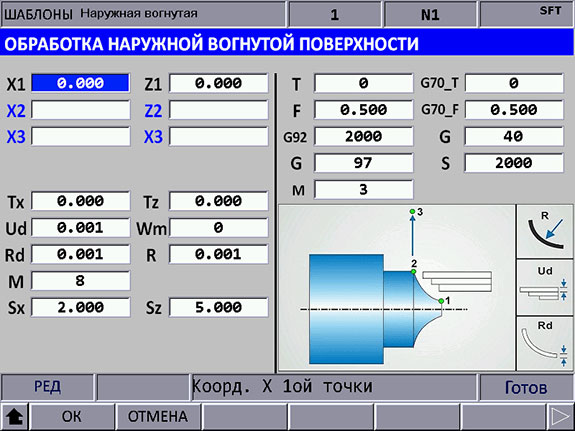 |
- X1, Z1 – координаты первой точки
- X2, Z2 – координаты второй точки
- X3, Z3 – координаты третьей точки
- Tx, Tz – координаты для смены инструмента
- Ud - глубина резания (X)
- Wm – настройки резания (0 – грубая + финишная, 1 – грубая, 2 – финишная)
- Rd– финишный допуск
- R – радиус дуги
- M – номер М-команды для подачи СОЖ
- T – номер инструмента для грубой обработки и его корректор
- G70_T – номер инструмента для финишной обработки
- F – скорость подачи для грубой обработки
- G70_F – скорость подачи для финишной обработки
- G92 – ограничение скорости шпинделя
- G (справа) – компенсация радиуса инструмента (40 – отключение компенсации, 41 – компенсация слева, 41 – компенсация справа)
- G (слева) – контроль скорости шпинделя (96 - постоянная скорость резания, 97 – постоянная скорость)
- S – скорость шпинделя
- M – направление вращения шпинделя
|
Внешний контур обработки
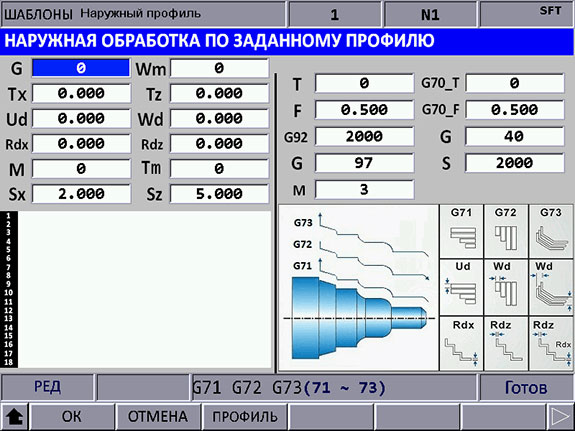 |
Внутренний контур обработки
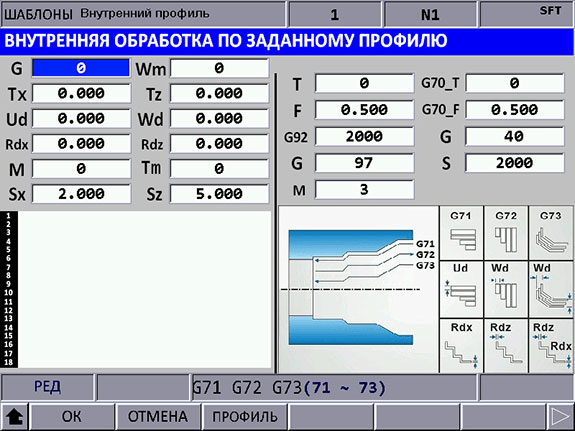 |
- G – G-код цикла обработки G71, G72, G73
- Wm – настройки резания (0 – грубая + финишная, 1 – грубая, 2 – финишная)
- Tx, Tz – координаты для смены инструмента
- Ud - глубина резания (X)
- Wd - глубина резания (Z)
- Rdx, Rdz – допуск по X, Z
- M – номер М-команды для подачи СОЖ
- Tm – количество циклов
- T – номер инструмента для грубой обработки и его корректор
- G70_T – номер инструмента для финишной обработки
- F – скорость подачи для грубой обработки
- G70_F – скорость подачи для финишной обработки
- G92 – ограничение скорости шпинделя
- G (справа) – компенсация радиуса инструмента (40 – отключение компенсации, 41 – компенсация слева, 41 – компенсация справа)
- G (слева) – контроль скорости шпинделя (96 - постоянная скорость резания, 97 – постоянная скорость)
- S – скорость шпинделя
- M – направление вращения шпинделя
|
Резьба метчиком
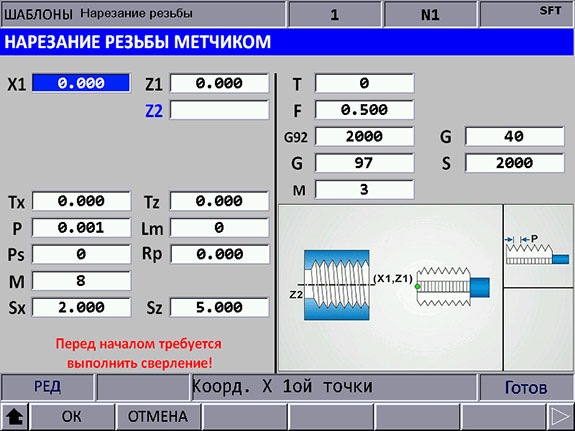 |
Создание профиля обработки через экран РЕДАКТОР ПРОФИЛЯ
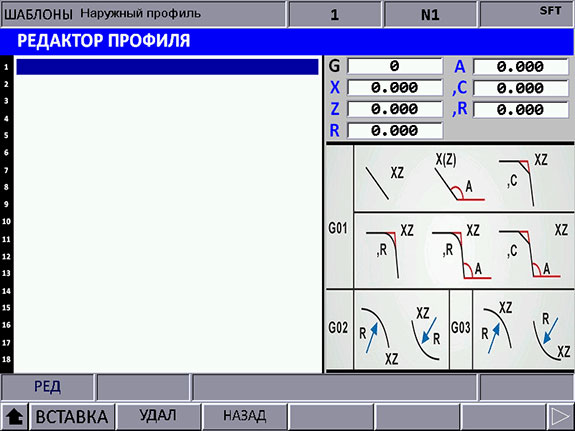 |
- X1, Z1 – координаты первой точки
- Z2 – координата второй точки
- Tx, Tz – координаты для смены инструмента
- P – шаг резьбы метчика
- M – номер М-команды для подачи СОЖ
- T – номер инструмента для грубой обработки и его корректор
- F – скорость подачи для грубой обработки
- G92 – ограничение скорости шпинделя
- G (справа) – компенсация радиуса инструмента (40 – отключение компенсации, 41 – компенсация слева, 41 – компенсация справа)
- G (слева) – контроль скорости шпинделя (96 - постоянная скорость резания, 97 – постоянная скорость)
- S – скорость шпинделя
- M – направление вращения шпинделя
|
- G – выбор типа интерполяции (G1, G2, G3)
- A – угол поворота по оси A (G1)
- X, Z – координаты точки
- С – фаска (градусы)
- R- радиус скругления (G1)
|